The Schiphol Cargo community’s Milk Run initiative has reduced C02 emissions at the airport by 30% and resulted in 3000 fewer truck movements in its first year.
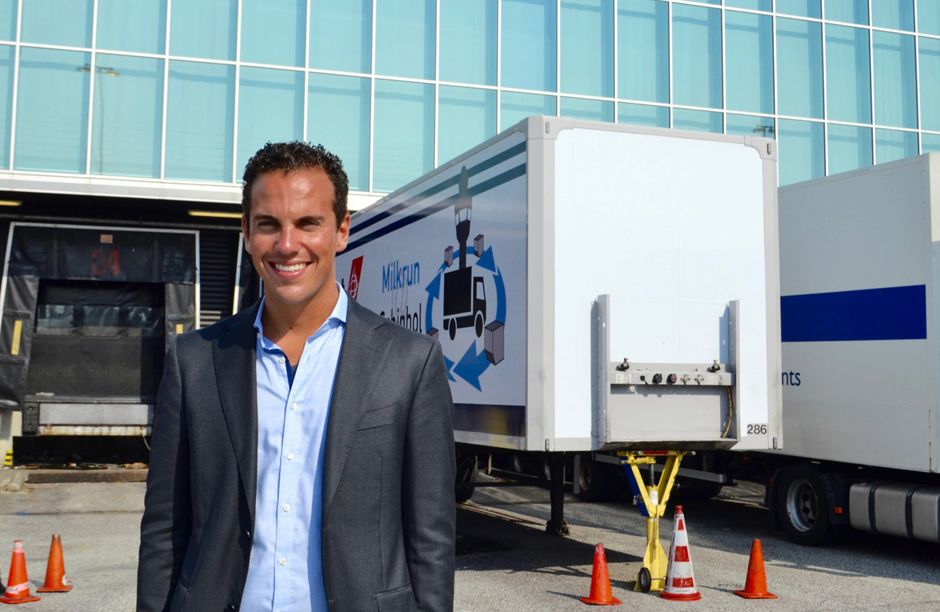
Published on: 26 September 2016
The group has just welcomed its 17th member and has embarked on a pilot scheme to test the initiative’s viability for exports. We caught up with Thierry Huizing, of Air Cargo Netherlands, who manages the project to find out how close collaboration can benefit our whole community and add value for customers.
Why was the Milk Run initiative launched?
I am proud to say that the Milk Run is the result of a partnership between Air Cargo Netherlands (ACN) and two graduate students who were on their work placements with us. It just goes to show that, with a cargo community such as Schiphol, every member has value to add. They were tasked with reporting on how ACN could tackle increasing emission levels, and identified the need to decrease traffic between the Ground Handlers (GHAs) and the forwarders. We realised we needed to be more collaborative in order to decrease truck movements and GHA waiting times and cut CO2 emissions from the engines of trucks waiting in line. We thought, this sounds interesting, let’s go for it, and the results of our three-month long pilot were positive and promising.
How would you describe your role within Milk Run?
I lead the project support team, which branches into operations and communications. I make sure that we are effectively communicating our objectives, achievements, and developments to potential and current members, and all of our customers. My team and I also spend our time investigating plans for expansion, and looking at how we can incorporate new concepts into the structure we already have. We then plan and implement steps for trialling these new concepts. Critically, we are responsible for keeping our operations at the high quality level our customers expect when they use the services of ACN and Schiphol Cargo.
Who are your members, and what have their reasons been for getting on board?
We started with five members – Menzies, a GHA, Bos Logistics, a trucker, and three forwarders, Panalpina, DHL and Nippon Express, all major players. Our newest member is CEVA Logistics who joined in March this year.
Handlers have seen the advantages of the Milk Run because it means they are able to push freight directly on to the forwarders. This has a fantastic knock on-effect on their warehouse operations, and affords them a lot of extra available space.
Traditionally, a handlers’ warehouse space is divided to accommodate 1/3 import, 1/3 export, and 1/3 storage. It is a huge advantage that freight is spending less and less time on these shelves. We now see the Schiphol community forwarders utilising their warehouse space much more efficiently, and happily being able to communicate this to current and potential clients!
By having fewer truck movements and fewer CO2 emissions at every warehouse, it also helps them address their own congestion and environmental issues. Our forwarder members benefit from cost savings because of reduced waiting times at the warehouse. Drivers and vans waiting in line are stationary but that unproductive time still has to be paid for. The Milk Run reduces those driving costs because delivery to the airport can come at a fixed rate. Reducing fulfilment time means better customer service.
What kind of feedback / results have you received from members and customers?
We are able to report a 30% reduction in CO2 emissions per tonne of cargo, based on data from May 2015 – May 2016, and 3000 fewer truck movements in the first year of the Milk Run – that’s more than 50%!
Our innovative Milk Run web portal automatically provides us with fortnightly environmental performance data; we have the data at our fingertips 24/7, and are able to begin tracking new pilot initiatives as soon as they are implemented.
Perhaps most interestingly, we have seen significant increase in the average loading degree of our truck. The Netherlands Organisation for Applied Scientific Research (TNO) previously calculated that, at any time, only ¼ of a truck was filled – that’s only 2.5 tonnes. We have increased the load of each truck to six tonnes since the start of Milk Run, making each truck movement more efficient. The feedback from members keeps me confident that the reasons they have for joining soon bear fruit.
Nippon Express, who is participating in our new export trial, recently reported that their administrative and staffing burden has been hugely reduced now they no longer send their trucks to the ground handler.
Other forwarders have been able to cut out the planning and scheduling for their trucks at Schiphol completely – they need only select the freight, and sit back confident in the knowledge that it will be collected from the warehouse. Swissport has reported seeing improvement on their waiting times which they have been trying to address for some time. I am thrilled the Milk Run is providing Schiphol Cargo Community members with solutions!
What are the latest developments within Milk Run, and what can we expect for the near future?
This May, we embarked on a pilot with Nippon Express and Menzies to see whether the Milk Run could also work for export freight. Export is little more complex as it involves factors such as load deadline and flight closures. My team and I are currently looking closely at what worked, and what challenges have arisen. We will soon be announcing the next phase of this pilot.
A surprising development has been that trucking companies are now working with ground handlers who are not their clients, and we feel great that we have created a model for how true collaboration can contribute toward common goals.
The whole Milk Run project team are really encouraged by these results and are looking forward to an exciting year of developments in further decreasing costs and CO2, and increasing efficiency across the whole cargo community!
For more information on the Milk Run, contact Thierry on thierry.huizing@acn.nl or +31 (0) 20 316 39 40.